Product Description:
Funik PCD And CBN Inserts PCD CCGT PCBN CBN RNMN RNGN Insert
Diamond Cutter Blade For PCBN Cutting

Features:

Polycrystalline Diamond (PCD) and Cubic Boron Nitride (CBN) Inserts
in Machining Processes
Polycrystalline diamond (PCD) and cubic boron nitride (CBN) inserts
are advanced cutting tools that offer unique material properties,
making them popular in machining processes. Here are the key
features and applications of PCD and CBN inserts:
Features of PCD Inserts:
- Material Hardness: PCD inserts exceed the hardness of traditional carbide tools,
making them ideal for cutting non-ferrous materials.
- Wear Resistance: PCD's hardness contributes to excellent wear resistance, making it
suitable for prolonged tasks with minimal tool degradation.
- Thermal Conductivity: PCD has excellent thermal conductivity, aiding in heat dissipation
during machining, helping tool integrity and reducing the risk of
thermal damage.
- Surface Finish: PCD tools provide superior surface finish and dimensional
accuracy, necessary for high-precision applications.
- Chemical Stability: PCD is resistant to chemical reactions, making it suitable for
machining materials that may be reactive or abrasive.
- Low Friction: The low friction coefficient of PCD reduces the cutting forces
needed, allowing for high-speed machining.
- Versatility: PCD inserts can be used for various operations, including turning,
milling, and drilling, primarily on non-ferrous materials such as
aluminum, composites, and plastics.
Features of CBN Inserts:
- High Hardness: CBN is the second hardest material after diamond, making CBN
inserts suitable for cutting hard ferrous materials, including
hardened steels.
- Wear Resistance: CBN exhibits excellent wear resistance, especially in high-speed
machining environments.
- Thermal Stability: CBN can withstand high temperatures without significant
degradation, an advantage for cutting applications generating high
heat.
- Chemical Stability: CBN is chemically stable at high temperatures, crucial when
machining materials that may generate reactive conditions.
- Edge Strength: CBN inserts maintain edge integrity better than traditional
carbide tools when cutting hard materials, reducing the risk of
chipping or breaking.
- Cutting Efficiency: CBN tools allow for efficient chip removal and reduction in
machining forces, which may enhance productivity.


Applications:
PCD inserts are ideal for non-ferrous materials, while CBN inserts
are better suited for hardened steels and iron-based materials,
making them a common choice in automotive and aerospace
applications.
Comparison:
PCD is more expensive due to the diamond content and manufacturing
process, while CBN is somewhat less costly. Additionally, both
inserts offer prolonged tool life compared to conventional carbide
due to their hardness and wear resistance.
Conclusion:
PCD and CBN inserts are essential components in the modern
machining industry. Understanding the specific features and
benefits of each type can help manufacturers select the right
inserts for their machining needs, leading to greater efficiency
and superior performance.
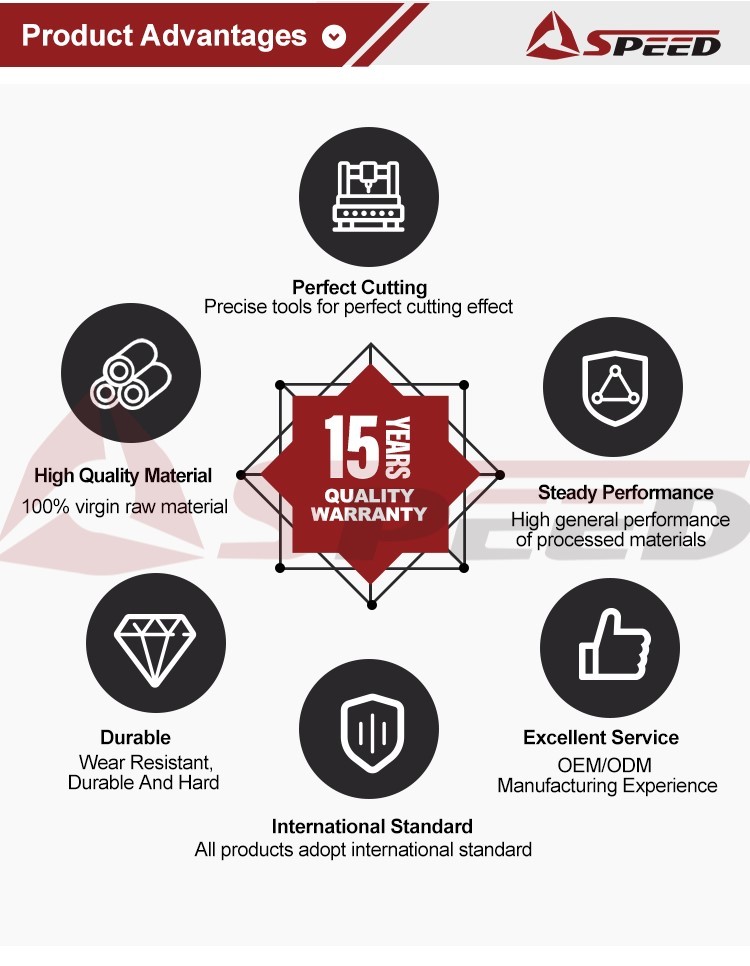
Technical Parameters:


The Technical Parameters of PCD and CBN Inserts
The technical parameters of PCD (Polycrystalline Diamond) and CBN
(Cubic Boron Nitride) inserts can vary based on their specific
application, geometry, coating, and manufacturer. However, some
common technical parameters are often evaluated when considering
these inserts. Here’s an overview of typically relevant parameters
for both PCD and CBN inserts:
PCD Insert Technical Parameters
- Material Composition: PCD inserts are made from diamond particles bonded with a metal
matrix, which may vary depending on the specific application.
- Hardness: Vickers Hardness: Typically > 6000 HV, depending on the
composition and manufacturing process.
- Thickness: Common Thickness: Ranges from 0.5 mm to 10 mm, depending on the
application.
- Grain Size: Average grain size: Can vary from 1 μm to several microns,
influencing wear resistance and toughness.
- Thermal Conductivity: Thermal Conductivity: Around 700-900 W/m·K, making it effective
for heat dissipation.
- Coating: Common coatings: PVD or CVD coatings may be applied to enhance
performance, depending on the material being machined.
- Edge Preparation: Geometry: Sharpened or honed edges can enhance cutting performance
in specific applications.
- Geometry: Insert shape: Various shapes available such as round, square,
triangular, and more, each optimized for particular cutting
applications.
- Chip Breaker Design: Available designs: Various chip breaker configurations can enhance
chip control and improve cutting efficiency.
CBN Insert Technical Parameters
- Material Composition: CBN inserts are typically made of cubic boron nitride in a solid
form, sometimes in combination with a binders such as cobalt or
ceramic.
- Hardness: Vickers Hardness: Typically 4500 - 5000 HV, providing excellent
wear resistance for hard materials.
- Thickness: Common Thickness: Similar to PCD inserts, ranges from
approximately 0.5 mm to 8 mm or more based on specific
applications.
- Thermal Stability: Operating Temperature: CBN can withstand temperatures up to about
1000°C (1832°F) without significant degradation.
- Coating: Common coatings: Often includes TiN, TiC, or Al2O3 coatings, which
can enhance wear resistance depending on the application.
- Edge Preparation: Geometry: Suitable edge preparations to optimize performance based
on the specific material and machining operation.
- Geometry: Insert shape: Various shapes are also available like square,
round, and octagonal, facilitating different types of machining
operations.
- Chip Breaker Design: Available designs: Various chip breaker geometries are used for
controlling chip flow and optimizing cutting conditions.
- Grain Size: Average grain size: Typically varies according to the
manufacturing process and intended use; finer grain sizes offer
better edge stability.
General Considerations for Both Inserts
- Insert Size: Standard insert sizes follow the ISO metric system (e.g., ISO ISO
8885:1993) and ANSI standard (e.g., ANSI B212).
- Flank Wear Resistance: Measurement of flank wear resistance is critical for assessing
tool life. This is sometimes measured in microns (µm) after
standard machining tests.
- Cutting Edge Strength: The cutting edge strength is essential for evaluating performance
under different cutting conditions and materials.
- Application Information: Each insert is often designed for specific cutting operations
(turning, milling, etc.) and materials (aluminum, hardened steel,
etc.).
Applications:
PCD inserts and CBN inserts both hold significant importance in
numerous industrial applications. These cutting tools are designed
to cater to specific materials and machining conditions that are
unique to the manufacturing process. Having a clear understanding
of the distinguishing features of these tools helps manufacturers
to fine-tune their processes and produce high-quality outcomes more
efficiently.
It is essential for users to carefully determine which insert is
best suited for the job at hand based on various factors such as
the material being worked on, the required tolerance levels, and
the desired surface finish. This will result in selecting the ideal
insert, leading to enhanced productivity, better process
optimization, and quality results.
Customization:
Brand Name: SPEED
Model Number: CBN PCD Inserts
Place of Origin: Zhuzhou, Hunan
Minimum Order Quantity: 10pieces
Price: 2.5USD
Packaging Details: 2pieces a box
Delivery Time: 5-7 days, large quantity 7-15days
Payment Terms: Paypal/TT/West Union/RMB/Visa
Supply Ability: 10000pieces
Application: Machining Of Cast Iron/Non-ferrous Metal/Hardened
Steel/Stainless Steel/Aluminum Alloy
Product Name: PCD CBN Insert
Edge Type: Sharp/Radius/Chamfer
Size: Customized
Processing Type: Cutting/ Grinding/ Polishing
Keywords: CBN Grooving Tools, Carbide Inserts, Carbide Insert
Support and Services:
Our PCD CBN insert product comes with comprehensive technical
support and services to ensure optimal performance and longevity.
Our team of experts is available to provide assistance with
installation, troubleshooting, and ongoing maintenance. We also
offer customization services to meet specific application
requirements. Our product support includes:
- Technical consultation and advice
- Installation guidance and support
- Customization services
- Training and education
- Product testing and evaluation
- Repair and maintenance services
- Warranty support
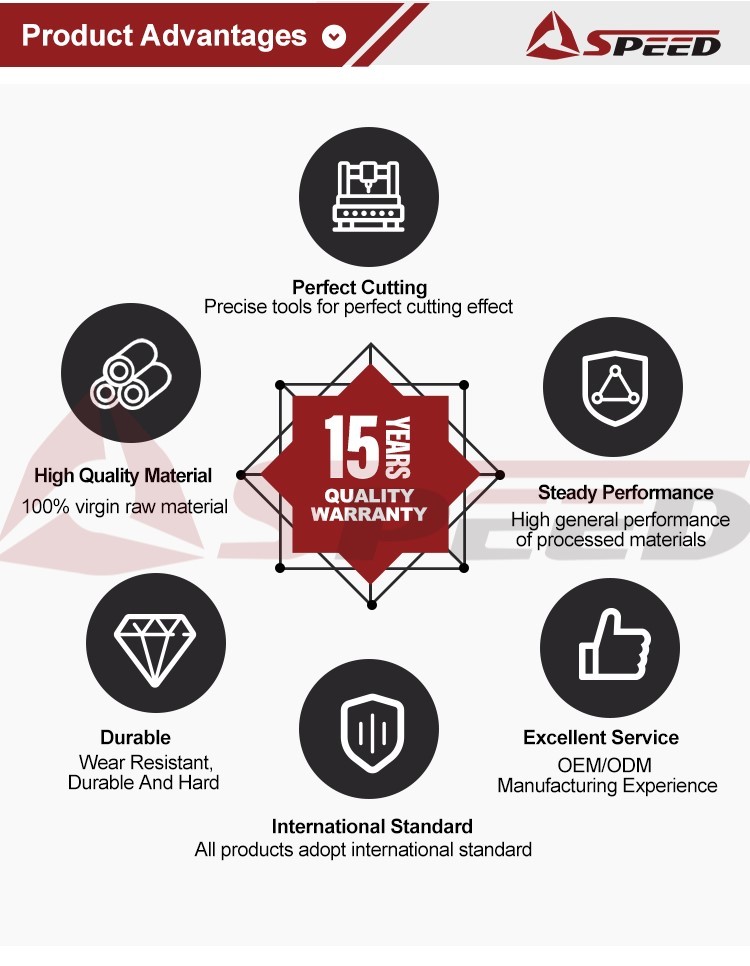
Packing and Shipping:
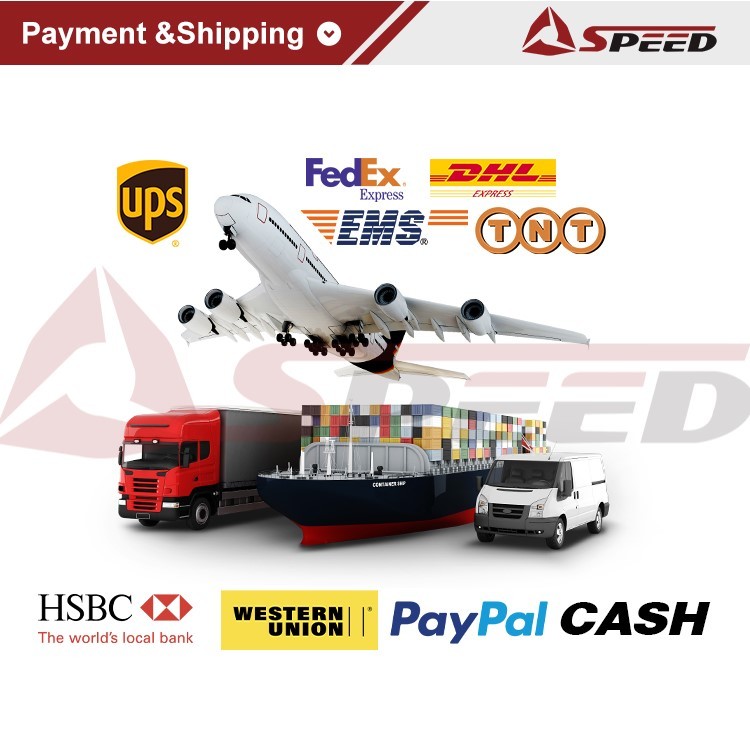
Product Packaging:
The PCD CBN Inserts will be carefully packed in durable plastic
containers to ensure maximum protection during shipping and
handling. Each container will be labeled with the product name and
specifications for easy identification and inventory management.
Shipping:
The PCD CBN Inserts will be shipped using a reliable and trusted
courier service to ensure timely and safe delivery. Shipping
options will be provided at checkout, allowing customers to choose
the method that best suits their needs and timelines.
